Project Description:
In March of 2020, one of Carter's Shared Milkrun customers, a large Tier 1 supplier, was forced to drastically reduce their volumes due to shutdowns caused by the Covid-19 pandemic. Carter Express Continuous Improvement Team took a proactive approach to pivot the suppliers logistics strategies and reduce their overall transportation costs.
Strategy:
Carter Express increased our communication frequency to daily calls with the customer's team on March 16th and continued those calls through June 19th, when volumes started to go back to more normal levels. Those calls accomplished the following:
- During the 3 months, over 100 temporary routes were created to consolidate different suppliers and optimize truck space
- Freight volume on our crossdocks were discussed daily and delivery trucks were only sent at the customers recommendation
- Every supplier pickup was discussed to determine the customer's need then Carter would strategize the most effective shipment method to meet that need.
- Every day, the team would review• the day before to discuss ways to continually improve& adapt to the ever-changing environment
Challenges:
- Communication & support with shared suppliers
- Predicting volume levels for other customers who had shut down completely
- Coordinating daily changes and a very hands-on approach with limited Carter staff
Result:
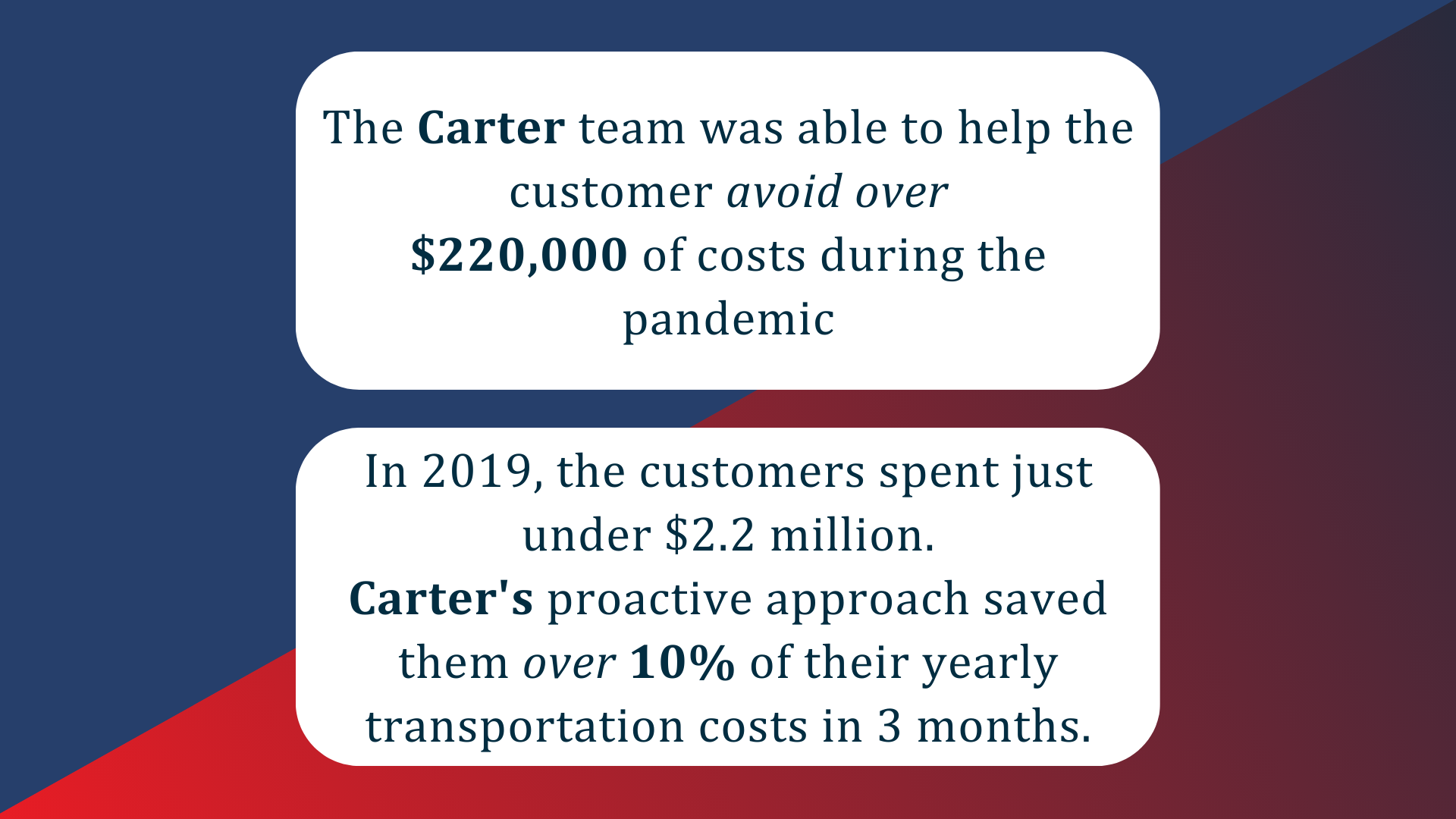
Carter overcame the challenges by keeping daily contact with our suppliers, having them submit daily volume information into the portal, contacting other customers weekly to get volume expectations and communicating daily across Carter departments to ensure everyone was working toward the most cost effective solutions for our customers.