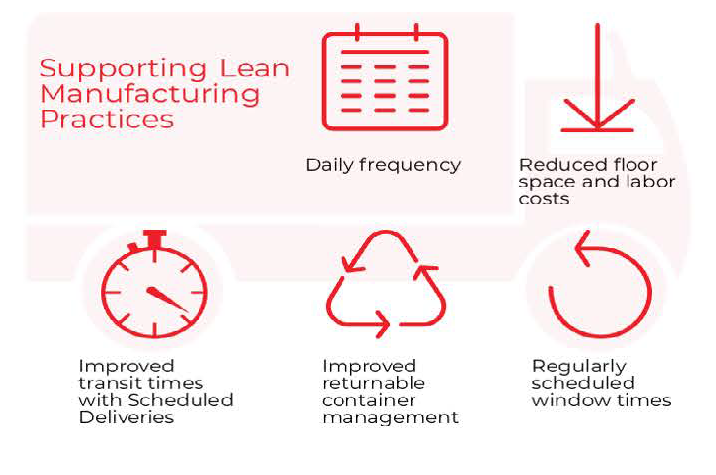
Project Description:
In 2014, a Tier 1 Supplier and global leader in the automotive industry, was operating their inbound material collections with two different logistics providers across their plant locations. This led to spiraling costs caused by inefficiencies and lack of visibility of inventories. dock congestion. poor carrier communication and difficulty in freight oversight.
Strategy:
To simplify our customer's logistics services and reduce overall logistics costs. Carter Express suggested they roll their entire network into the Carter Shared Milkrun System (prior to this discussion they had a little less than half of their network in the shared system)
To achieve our customer's goals, the Continuous Improvement Analysts at Carter Express built a network consolidation plan that worked with their existing system but combined freight with Carter's other customers to increase trailer cube and decrease spend.
The Carter Express team then started their weekly analysis on the network and continually optimizes routes and decrease costs.
Carter Express utilizes its proprietary split-bill methodology: this method allows our customer to only pay for the % of the route cost that equals the % of their weight of the trailer's overall freight.
To help convince our customer's management of the benefits of the change, Carter was able to offer a guaranteed annual transportation savings of $3M in the first two years.
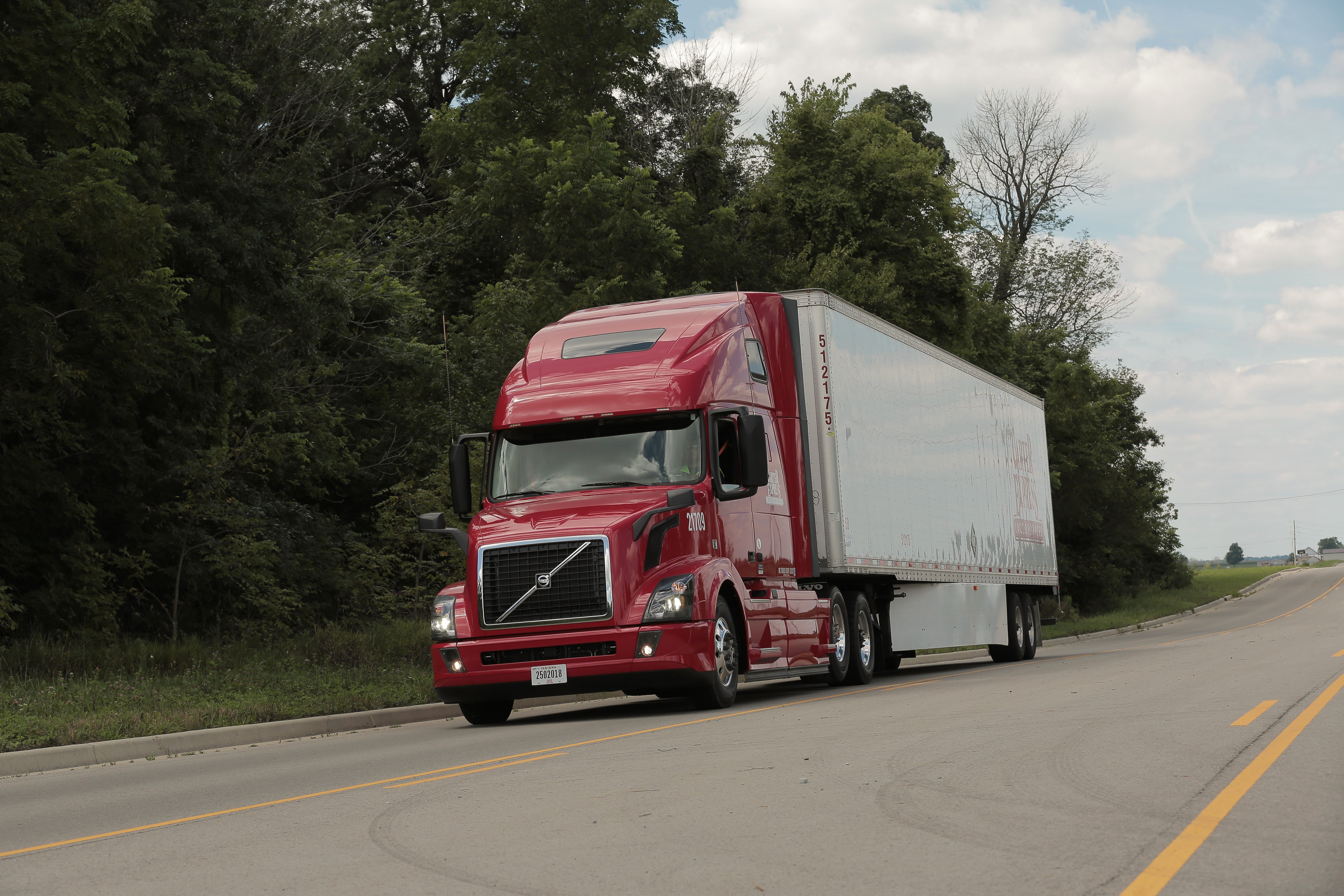
Challenges:
The Tier 1 Supplier's initial challenges included a lack of inventory visibility, cost overruns, dock congestion and poor carrier communication.
The challenges to the Carter Express team to implement the shared system included:
- verifying shipment data and supplier information
- convincing the plants of the need for a change in shipping methodology (more frequent shipments of lesser quantities)
- winter weather challenges as the implementation and changeover happened in January and February of 2014
Result:
Carter Express was able to meet the guaranteed $3M of savings in the first 9 months of implementation and saved our customer a total of S7.5M in the first 2 years.
Total savings in the 6 years since implementation equals $16.9M.
The Tier 1 has also significantly reduced its environmental impact due to the higher cube utilization of shipments and the decrease of overall trucks needed to run the network.